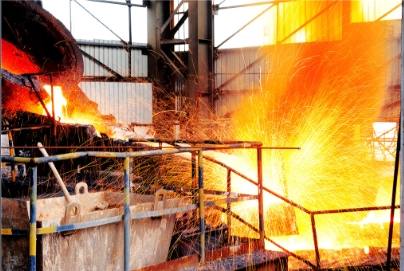
1 Supply
and Demand Situation and Trend of Raw Materials
1.1 Superior Titanium Ore
Rutile,
which has been deemed as a superior raw material for producing titanium dioxide
and titanium sponge, is generally the paragenesis with ilmenite, zircon and
other heavy minerals.
Only three
mining companies all across the world have the annual production capacity of over 10 X 104 tonnes,
among which Sierra Rutile Marketing Ltd., with the headquarters located in
Sierra Leone of Western Africa, accounted for 20% of the global supply, while
Australia takes up 50%. In 2014, the global rutile output was 74.5 x104 tonnes.
Globally,
with the declining reserves and quality grade of the rutile, and the increasing
of orebody complexity, the growth of the consumption of the titanium dioxide
pigment exceeded the supply of rutile. Moreover, both the rapid growth of the
demand from the aviation field on titanium and the titanium white production
through the emerging chlorination process in China would greatly increase the
demand on rutile.
1.2
Titanium Sponge
It is
estimated that the production of global titanium sponge has exceeded 30 X104 tonnes. With the
production capacity of 15 X104 tonnes and over 10 titanium sponge
producers, China has been the largest country across the world in terms of the
capacity of titanium sponge. Currently, China is implementing industrial
integration with the expectation of reducing the annual production capacity to 10
x104 tonnes, and thus a proportion of small-scale, low-efficiency,
and poor-quality producers of titanium sponge would be eliminated.
The
titanium sponge output of China was about 6. 8 x104 tonnes in 2014,
while both in 2012 and 2013 the output was 8. 1 x104 tonnes, which took
up nearly 40% of the total supply of the globe and exceeded the sum total of
Russia, Kazakhstan and Ukraine. In the recent years, the export of titanium
sponge of China fluctuated violently, with the export of 1,000 tonnees in 2009,
1. 1 x104 tonnes in 2011, and 6,000 tonnes in 2014. In 2014, the
biggest market was South Korea with 36% of gross export of China’s titanium,
followed by the US with 28%.
The output
of the titanium sponge of VSMPO of Russia, the magnate of global titanium
industry, was 4 x104 tonnes in 2014, while the output of the company
exceeded 4 x104 tonnes both in 2012 and 2013, accounted for about
20% of the overall supply of the world.
As for
Japan, the output of titanium sponge was about 3 x104 tonnes in 2014 and was 3.5 x104 tonnes in 2013. In the recent years, the export of
titanium sponge of Japan has declined, with 3.1x104 tonnes in 2012 and 1.6x104 tonnes in 2014.
1.3 Waste
Material of Titanium
One of the
important channels for the supply of raw material of titanium is the waste
material of titanium. Each year, half of the waste material was used to provide
large amount of low-cost raw materials for producing titanium and titanium
alloy, and the other half was used for the ferrotitanium conversion or applied
in the other fields.
Matt
Schmink, vice-president of sales of Global Titanium Inc. (with the headquarters
located in Detroit), analyzed the trend of the demand on ferrotitanium. In
2014, the gross output of steel exceeded 1.6 billion tonnes all across the
world, among which the consumption of titanium was about 73,684 tonnes--mainly
applied as alloy addition in the form of ferrotitanium or waste titanium to
produce carbon steel and stainless steel. 80% of the steel with the addition of
titanium was used in manufacturing automobile and electric appliance.
According
to Matt Schmink, the titanium consumption in steel industry would remain in
about 70,000 tonnes by the year of 2020. The ferrotitanium market would enjoy a
good supply and demand situation in the next few years and it’s highly possible
to face a buyer's market, which would therefore bring price downturn in waste
titanium and ferrotitanium. The titanium industry may have to increase the
utilization ratio of waste titanium and at the same time develop new market, so
as to offset the situation of oversupply.
1.4 Master
Alloy
Master
alloy is also an important raw material of titanium alloy. The addition of the
master alloy in processing could improve the heat resistance and corrosion
resistance of titanium, so as to satisfy some particular purpose or requirement.
As for master alloy, the vanadium and molybdenum took up 90% of the annual
gross demand. Due to the special purpose of the usage of master alloy, the
quality is of crucial importance, and the cost relies on the market price of
the raw materials.
Terry T.
Perles, president of MoTiV Metals LLC (subsidiary corporation of Bridgeville),
has estimated that the global vanadium consumption of 2015 would be 9. 3 x104 tonnes, among which the steel industry accounted for 92%, titanium industry 5%,
and chemical and energy reserve industries 3%; moreover, the global molybdenum
consumption was 238,350 tonnes in 2015.
2. Demand on the Aviation Market and Its
Development
2.1 Estimation from Authorities of Titanium
Industry
Wade Leach, vice-president of market and
product management of ATI, continues to favor the titanium market towards the
future commercial aircraft. His expectation was based on the analysis on the
trends of the profitability of airlines, cost of fuels, and the ever-increasing
circular flow of passengers; what’s more, the output of the newly designed
airplanes with the usage of large-amount titanium is increasing in a short run.
Although
the situations in Greece, Syria, and China are still in uncertain, the profitability of the airlines around the globe enjoyed a
tremendously increase in 2015. Globally, the quantity of commercial aircraft
would amount to 5 x 104 by the year of 2035, according to Wade Leach, this number is as twice as that of 2014 (2.5 x104). The supply chain of the production of airplane is globalizing,
the new titanium alloy with more superior properties is in research, and the
titanium alloy 3D printing-reinforced materials manufacturing technology is
making rapid progress, all of those development would make the titanium alloy
remain to be a superior choice for the materials of commercial airplane.
According
to Henry S. Seiner,
vice-president of the business strategy of Timet, the gross output of aero-engine
was 3,160 in 2014, among which the CFM International (Joint Venture of Snecma
and GM) was the dominant producer, followed by GM, IAE (International Aero
Engines), Rolls-Royce, and HP.
Titanium
alloy would remain to be the major material for the compressor of the jet
engine, for example, the blades of the fans, and the titanium-aluminum alloy,
as the substitute of Ni-based superalloy, is marching to the field of combustor
of turbofan jet. However, the role of titanium alloy, which refers to the
candidate material of airplane manufacturing, is challenged by composite
materials and aluminum alloy.
Eric
Roegner, president of titanium and engineering products and defense department
of Alcoa, believed that although defense budget the US and its general
expenditure is stable, the cost in defense aviation is remarkably increasing.
For example, the F42 and F-35 warplanes involved big titanium projects.
Moreover, the application of titanium in the fuselage of warplane has rapidly increased;
the proportions of titanium in F-22, F-35, and V22 are 32%, 25%, and 16%,
respectively. The unrest situation would propel the growth in the demand on
titanium in the defense aviation fields, especially in the Middle East.
The
innovation in materials and its manufacturing methods are also very important
in promoting the application, for example, the research on the components and
parts of titanium-aluminum airplane, the development on the 3D printing, and
the innovative adhesive, welding, and technologies would all together to
promote the applying of the titanium in airplane. In security and military
field, the titanium is challenged by aluminum-lithium alloy, as the
aluminum-lithium alloy, which also has the property of corrosion resistance,
has been defined as the substitute of titanium in composite-intensive airplane.
Michael
Metz, president of VSMPOTirusU.S., conducted a review and outlook on the
titanium market of 2010-2021 in Russia and given a list of data, including the
general titanium consumption, the consumption of the fields of aviation,
shipbuilding, power-generating, and general industries in the period ranged
from 2010 to 2014, moreover, he also estimated the demand on titanium from 2015
to 2021.
According
to Metz, general demand of Russia on titanium would amount to 1. 31 x104 tonnes by 2021, which is almost equal to that of 2014,
but slightly higher than that of 2015 (1.25 x104 tonnes). From the
perspective of industries, the demand from aviation industry was nearly 7,000
tonnes in 2015, while in 2021, that number would increase to 8,000 tonnes; the
demand from the shipbuilding industry was 3,600 tonnes, and it will reduce to
2,900 tonnes in the period from 2016 to 2017, finally by 2021 the demand would
keep in the level of 2,400 tonnes; in terms of the industries of non-ferrous
metal, equipment, and chemical engineering, the demand in 2015 was 840 tonnes
and it will increase to 1,000 tonnes by 2021; in power generation, the demand
seems to fluctuate frequently--450 tonnes of 2015, ,700 tonnes of 2016, 950 tonnes
of 2017, 700 tonnes of 2018-2020, 420 tonnes of 2021; as for the other
industries, the demand from 2015 to 2021 would keep in the level of 760 tonnes.
President
of Toho Titanium and the Titanium Association of Japan offered the sales volume
of titanium manufactured lumber of the period ranged from 1981 to 2014. The
gross sales of titanium products of Japan began to increase from 2013, and it
is expected to increase to 1.5 x 104 tonnes by 2015,
slightly higher than that of 2014; moreover, the overseas sales have all the
way much better than the domestic market since 2009 in Japan.
2.2
Analysis from Authorities of Aviation Industry
According
to Airbus, there would be 29,000 newly constructed passenger planes and cargo
planes to come into use by 2032, with gross values of nearly USD4.4 trillion. Thomas
T. Cochelin, purchasing manager of titanium and special alloys of Airbus,
mentioned that the company consumed 30 tonnes of titanium per day in 2014, as
the titanium application of the new model of A350XWB is 180 times of A330, it
is expected that the titanium consumption of the Airbus in 2020 would be 180%
of that of 2013.
According
to William T. Shaffer, the materials and standards inspector general of Boeing,
there would be 38,050 new airplanes deliver for commissioning by 2034, among which
the biggest market would be Asia (14,300), followed by North America (7,890)
and Europe (7,320).
From Shaffer’s
introduction, as the commercial airplane 747-8 of Boeing has 6 million
components and parts in total, 777 has 3 million, and 737 has 400 thousand, the
components and parts the company has purchased each year amounted to 1 billion,
with the cost of USD43 billion and suppliers of 5,400.
According
to Waldir Gomes Concalves, senior vice-president of global customer support and
service of Embraer Commercial Aviation, there would be 6,350 commercial
airplanes of 70—130 seats deliver into commissioning all across the world in
the next 20 year, with the gross values of USD300 billion, among which the US
would take up the biggest share (2,068, 32%), followed by Europe (1,160, 18%)
and China (1,020, 16%); while in the next 10 years, there would be 9,250
official airplanes come into commissioning, valued USD265 billion, among which
North America would account for the biggest market share (50%); the EMB-314 of
Embraer would amounted to 300 by 2020, among which 190 have already delivered,
and the KC-390 of the company would amounted to 700 by 2025.
*This article is edited and translated by CCM. The original one comes from Titanium Industry Progress.
About CCM:
CCM is the leading market intelligence
provider for China’s agriculture, chemicals, food & ingredients and life
science markets. Founded in 2001, CCM offers a range of data and content
solutions, from price and trade data to industry newsletters and customized
market research reports. Our clients include Monsanto, DuPont, Shell, Bayer,
and Syngenta. CCM is a brand of Kcomber Inc.
For more information about CCM, please
visit www.cnchemicals.com or get in
touch with us directly by emailing econtact@cnchemicals.com or calling +86-20-37616606.